Third Party Inspections
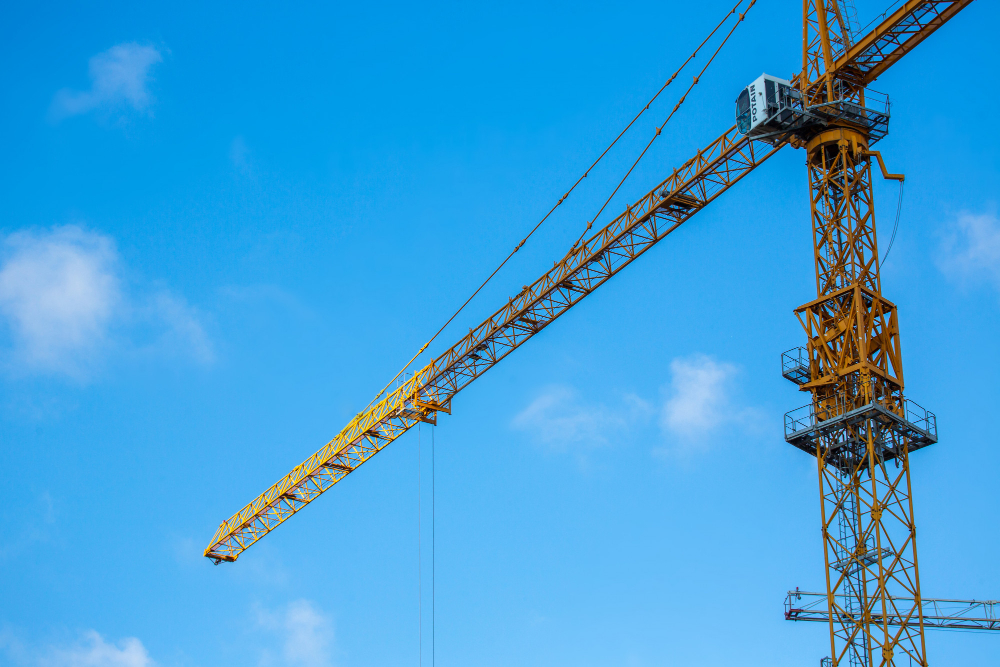
Third Party Inspections Hub
Third Party Inspections
SAFETY technical SERVICES is a full member of Lifting Equipment Engineers Association LEEA and an inspection body accredited by GAC for ISOIEC 17020. We provide various inspections, testing and certification for all the lifting equipment and loose lifting gears. We have a team of LEEA approved competent lifting equipment inspectors who can conduct six monthly, twelve monthly and forty eight monthly inspection at Lifting Division our rigging yard in Muscat or at your location. Inspections are carried out in compliance to ISO/IEC 17020, LEEA codes of practice, Lifting Operations and Lifting Equipment Regulations LOLER, Provision and Use of Work Equipment Regulations PUWER, BS EN Standards & Petroleum Development of Oman – PDO guidelines and procedures.
Lifting Inspections
SAFETY technical SERVICES and Inspections offers comprehensive inspection, testing, and certification services for lifting equipment and loose lifting gears. Being a full member of the Lifting Equipment Engineers Association (LEEA) and accredited by GAC for ISO/IEC 17020 demonstrates a commitment to maintaining high standards in safety and quality.
Our team of LEEA-approved competent lifting equipment inspectors ensures that inspections are conducted according to various regulations and standards, including ISO/IEC 17020, LEEA codes of practice, Lifting Operations and Lifting Equipment Regulations (LOLER), Provision and Use of Work Equipment Regulations (PUWER), BS EN Standards, and guidelines from organizations such as Petroleum Development of Oman (PDO).
Offering inspections at both your rigging yard in Muscat and clients’ locations provides flexibility and convenience, ensuring that lifting equipment is regularly checked and compliant with relevant regulations and standards. This proactive approach helps enhance safety and efficiency in operations involving lifting equipment and contributes to overall risk management efforts.
- Lifting inspections involve the examination of equipment used for lifting heavy loads, such as cranes, hoists, slings, and shackles.
- These inspections are conducted to ensure that lifting equipment is in good working condition, free from defects, and capable of safely lifting the intended loads.
- Inspections may cover visual checks, functional testing, and non-destructive testing methods to detect any signs of wear, damage, or structural weakness.
- Compliance with regulations such as LOLER (Lifting Operations and Lifting Equipment Regulations) and PUWER (Provision and Use of Work Equipment Regulations) is typically ensured during these inspections.
- Regular inspections, often performed at intervals of six months, twelve months, or forty-eight months, help identify issues early and prevent accidents or equipment failures.
- Loose Lifting Gears: This includes various lifting accessories such as shackles, hooks, slings, and eyebolts etc.
- Spreader/Lifting Beam: Used for lifting loads that require multiple attachment points.
- Manual and Electric Chain-Wire Hoists: For lifting and moving heavy loads in industrial settings.
- Hydraulic Jacks and Systems: Used for lifting and supporting heavy equipment or structures.
- Mobile Crane/Crawler Crane: Versatile lifting equipment used in construction, maintenance, and other industrial applications.
- Tower Crane: Tall, fixed lifting equipment commonly used in construction projects.
- Lorry Loader Crane: Mounted on trucks for loading and unloading heavy cargo.
- Overhead Crane: Suspended from a beam or gantry for lifting and moving heavy loads within a facility.
- Deck/Pedestal Marine Crane: Used on ships and offshore platforms for handling cargo and equipment.
- RTG/Quay Cranes: Used in ports for container handling.
- Side Boom Crane: Designed for pipe laying and other specialized lifting tasks.
- Offshore Crane: Specifically designed for use in offshore environments, often on oil rigs or platforms.
- Industrial Forklift Trucks/Telehandlers: Used for material handling and lifting in warehouses, construction sites, and industrial facilities.
- Reach Trucks and Lifters: For high-level stacking and picking in warehouse environments.
- Vehicle Lifts (2,4 Post): Used for lifting vehicles for maintenance and repair.
- Suspended Access Equipment (Cradles): Used for accessing and working at height on buildings and structures.
- Monorail/Runway Beams: Used for overhead material handling and movement.
- Concrete Mixers and Pumps: Equipment used in construction for mixing and pumping concrete.
- Winches: Used for lifting, pulling, and hoisting heavy loads.
- Air Compressors and Receiver: Providing compressed air for various applications.
- Offshore/Onshore Containers, Baskets, Skips: Containers and baskets used for transporting equipment and materials.
- Earth Moving and Construction Machinery: Equipment such as excavators, bulldozers, and loaders used in construction and earthmoving tasks.
- Rig Handling Tools: Specialized tools and equipment used in rigging operations.
- Towing and Mooring Sets: Equipment used for securing vessels and offshore structures.
- Gangways and Accommodation Ladders: Access equipment for boarding ships and offshore installations.
- Bollard Pull Test: Testing the pulling capacity of bollards, often used in maritime applications.
- Safety Harness and Sets: Personal protective equipment for working at height.
- Non-destructive Inspection (VT, PT, MPT): Inspection methods such as visual testing, penetrant testing, and magnetic particle testing for detecting defects without damaging the equipment.
- Destruction Tests (Up to 200 Tons): Testing the load-bearing capacity of materials or structures through destructive means.
Rig Inspections
When conducting rig inspections, particularly concerning lifting gears and winches, safety and compliance are paramount. Here’s how inspections for lifting gears, pad eyes, and various winches on a rig are typically conducted:
- Lifting Gears and Pad Eyes:
- Visual Inspection: Trained inspectors visually examine all lifting gears and pad eyes for signs of wear, damage, or deformation. This includes shackles, hooks, slings, and other accessories.
- Load Testing: Depending on regulations and industry standards, periodic load testing may be required to ensure lifting gears and pad eyes can handle the intended loads safely.
- Certification: Lifting gears and pad eyes are inspected for certification labels or markings indicating compliance with relevant standards and regulations.
- Documentation: Inspection reports are generated detailing the condition of lifting gears and pad eyes, any defects found, and recommendations for corrective action. Records are maintained for regulatory compliance and audit purposes.
- BOP Winches, Utility Winches, Man Riding Winches, Monkey Board Winches:
- Visual Inspection: Inspectors visually examine all winch components, including cables, drums, brakes, pulleys, and controls, for signs of wear, corrosion, or damage.
- Functional Testing: Winches are tested under load to ensure proper operation and functionality. This may involve deploying and retrieving loads to verify the winch’s performance.
- Safety Features: Inspectors check for the presence and functionality of safety features such as emergency stop mechanisms, overload protection, and interlocks.
- Compliance Verification: Winches are inspected to ensure compliance with relevant regulations, industry standards, and manufacturer specifications. This includes load capacity ratings, electrical safety standards, and structural integrity requirements.
- Operational Checks: Inspectors may observe winch operations during normal rig activities to identify any issues or concerns with performance.
- Documentation: Inspection reports document the condition of each winch, any deficiencies noted, and recommendations for corrective action. Records are maintained for regulatory compliance and future reference.
- Rig Major Inspection (CAT III, CAT IV) as per API RP 4G
- BHA Inspection Services (Drill Collar, HWDP, Subs Tools) as per API RP7G-2, DS1 CAT III, CAT IV
- Handling & Hoisting tools Inspection as per API RP 8B
- Magnetic Particle Inspection Services
- Ultrasonic Thickness Gauging
- Liquid / Dye Penetrant Inspection
- Drilling & fishing tool Inspection services as per DS I & NS 2
- Temporary Pipe Inspection with Load Shoulder Gauge as per PDO PR 1448, API 53
- Well Control Verification with Tagging as per API 53
- Calibration & Maintenance of fixed gas detection, fire alarm system Onsite
- Boroscope Services
- Sand Blasting & Coating Services
By conducting thorough inspections of lifting gears, pad eyes, and winches on rigs, operators can ensure the safety, reliability, and regulatory compliance of lifting operations. Early detection of issues allows for timely maintenance or repair, minimizing the risk of accidents and downtime on the rig.
DROPS
Bottom of Form
It’s impressive that STSI has been utilizing DROPS (Dropped Object Prevention Scheme) awareness and prevention formats, along with the DROPS Inspection Guide, for several years within the oil and gas industry. Here’s how your approach to drops inspection works:
- Objective:
- The primary goal is to prevent potential accidents caused by dropped objects, which can pose significant safety risks in oil and gas operations.
- Scope of Inspection:
- STSI conducts comprehensive surveys to assess the risk of dropped objects across various structures and areas within oil and gas facilities.
- This includes inventorying equipment within structures, assessing their integrity, and recommending secondary retention methods where necessary.
- Methodology:
- The inspection process involves examining all items and attachments to structures to ensure they are properly secured and in fit-for-purpose condition.
- Both primary and secondary retention devices are evaluated to prevent objects from falling.
- Special attention is given to assessing any corrosion on structures, fixtures, and equipment, as corrosion can weaken attachment points and increase the risk of drops.
- Reporting:
- Inspection reports provide a detailed inventory of equipment within structures, including an assessment of integrity and recommendations for secondary retention methods.
- The severity, location, and areas of concern regarding dropped object risks are identified and detailed in the report.
- Individual photos and specific recommendations are included to facilitate understanding and action.
- Risk Mitigation:
- Recommendations provided in the inspection report help mitigate the risk of dropped objects by ensuring that appropriate retention methods are in place and that equipment is properly maintained.
- By identifying areas of concern and providing actionable recommendations, STSI assists clients in proactively addressing potential hazards and enhancing overall safety performance.
Overall, STSI’s approach to drops inspection demonstrates a proactive commitment to safety and risk prevention in the oil and gas industry. By leveraging industry best practices and expertise, STSI helps clients mitigate the risk of dropped objects and promote a safer working environment.
NDT: Non Destructive Testing Services STSI is a leading NDT service provider offering a wide range of services in both Up-Stream & Down-Stream, This includes: Comprehensive Rig Inspections, quality control, Our team of professionally qualified and certified technician are well versed and experienced to perform conventional and advanced NDT inspection. Our team of technicians is available on a 24 x 7 standby call irrespective of environmental conditions.
In MT the part is magnetized. Finely milled iron particles coated with a dye pigment are then applied to the specimen. These particles are attracted to magnetic flux leakage fields and will cluster to form an indication directly over the discontinuity. This indication can be visually detected under proper lighting conditions.
PT uses a liquid with high surface wetting characteristics that is applied to the surface and allowed to seep into defects and then excess liquid is removed.
A developer is applied the trapped penetrant is pulled out of the defect where it can be seen.
A visual inspection is then performed.
The penetrant used is often loaded with a fluorescent dye and the inspection is done under UV light to increase test sensitivity.
Electromagnetic testing is a general test category that includes Eddy Current testing (ECT), Alternating Current Field Measurement (ACFM) and Remote Field testing. While magnetic particle testing is also an electromagnetic test, due to its widespread use it is considered a stand-alone test method rather than an electromagnetic testing technique. All these techniques use the induction of an electric current or magnetic field into a conductive part, then the resulting effects are recorded and evaluated.
VT is the visual observation of the surface to evaluate the presence of surface discontinuities. Corrosion, misalignment of parts, physical damage and cracks are some of the discontinuities that may be detected by VT.
VT is the most used test method in industry as most test methods require that the operator look at the surface of the part being inspected. VT inspections may be by direct looking, or maybe by use of optical instruments such as magnifying glasses, mirrors, borescopes, and remote Viewing.
UT uses the same principle as is used in naval SONAR and fish finders. Ultra-high frequency sound is introduced into the part being inspected and if the sound hits a material with a different acoustic impedance (density and acoustic velocity), some of the sound will reflect to the sending unit and can be presented on a visual display.
RIG and Hoist Inspection: STSI Rig & Hoist Inspection Services help prevent equipment downtime, boost productivity and enhance safety. We provide yearly Catogory III or Category IV Inspections at the customer facility to ensure its fitness for use which is done by experienced welding and NDT Inspectors
One of our main specialties is the planning and execution of the 5 yearly certification of the derrick drilling equipment, which is done according to the manufacturer’s specifications and as per API recommendations. We have multidisciplined, inspection teams provided with a thorough knowledge and proven experience in this critical scope.
For each equipment inspection, we perform sand blasting, inspection, assessment. Find below a list of the pieces of equipment usually included, but not limited to;
- Mast and Substructure
- Top Drive, DDM and Gear Box
- Dolly Assembly
- Travelling Block
- Crown Block, Cluster Assemblies and Housing replacement
- Fast and Dead Line Rocker Arms and Sheaves
- Pipe Racking System
OCTG / Tubular Inspection
Drill Pipe Inspection
Our drill pipe inspection services help ensure pipe is fit-for-service, improve drilling performance, and extend your drill pipe life cycle. We provide the necessary inspections for all drilling operations, including deviated and horizontal wellbores. Our comprehensive drill pipe inspection program assists in maximizing your drill string performance.
Ultrasonic (UT), electromagnetic inspection (EMI), magnetic particle (MPI), and multiple dimensional checks are used to detect defects that are crucial to preventing downhole failures, saving you potential downtime and reducing costs.
Our inspections are performed in-plant or in the field using proprietary Tuboscope inspection equipment and software. All tool joint and tubular inspection services are carried out in accordance with standards such as API, DS-1, and NS-2.
STSI inspection equipment used:
- New Tech ( Tech Scope EZT-II )– detects service-induced defects, such as cracks, pitting, holes, and corrosion
- New Tech ( Tech Scope EZW-II )– detects service-induced defects, such as cracks, pitting, holes, and corrosion EMI wall monitoring
Casing and Tubing Inspection:
STSI Inspection provides OCTG [ NEW & USED] Inspection, in compliance with API Specification. STSI is equipped with state of art custom-built yard-based Inspection units Four Function detection systems for Tubing and Sucker Rods.
- 2-3/8” To 5-1/2” Tubing & 4-1/2” To 30” Casing Specifications: – API Standard Manufacture`s Specifications.
Scope of work:
- Internal and external Surface Inspection
- Full-Length Drifting
- Visual Thread Inspection
- Residual Field Magnetic Field induction
- Coupling Removal and Re-installation
- Internal Coating
- Four Function Inspection
- Internal External Pipe Cleaning
BHA Inspection
Comprehensive tubular inspection service of new or used equipment to ensure reliable and safe operation of a drilling operation at the rig. STSI thoroughly inspect BHA and according to client requirement or and per the specified standard with highest quality in accordance API-RP-7G and DS-1 standards. We can provide a Mobile Refacing kit, so we can do the seal repair onsite, saving logistics and extra cost.
Our certified inspectors comply with ASNT procedures and standards, offering inspection services for drill stem bottom hole assemblies including;
- Heavy Weight Drill Pipe
- Drill Collars
- Subs
- Stabilizers
- Down Hole Assembly – BHA
- Special tools, MWD, Mud motors/turbines, fishin
Sucker Rod and Continuous Rod Inspection
STSI comprehensive sucker rod inspection and reclamation services are designed to maximize sucker rod life cycle as well as reduce downtime and well operating expenses. Our proper inspection techniques identify which rods are suitable for further service, limited service, or which need to be removed from service and discarded. All inspections are performed by ASNT-qualified Level I and II inspectors.
Our critical inspection process for new and used sucker rods includes:
7/8” To 1-1/8” Sucker Rod & Polish & Pony Sucker Roads
Scope of Work
- High-Pressure water blasting to remove thick scale and the crude residue
- Full-Length Visual Inspection
- Visual Thread Inspection
- Full-Length EMI Inspection
- Full-Length Road Diameter verification
- Full-Length Rod Body Eddy Current verification for Hot Spot
- Fluorescent Magnetic Particle Inspection of Pin and Couplings
- Coupling Removal and Re-Installation
- External Coating
- Hard Stamping Internal Coating
- Color coding and Bunding
Pressure Testing and Well control
This is a specific scope mainly focused on well control equipment, especially for clients expecting difficult drilling conditions and well control risks. The concerned equipment are the following:
- BOPs (annular, single ram, double ram)
- Accumulator unit and associated equipment (bottles, hoses, remote panels…)
- Choke Manifold & remote choke control unit
- Choke line and its valves
- Kill line and its valves
- Mud cross, DSAs and Drilling spools
- Trip tank, PVT system, flow show paddel, gas detector
- Review of well control equipment Certificates (initial and original COCs)
- Review of well control equipment RE-Certification records
- Review of all related maintenance records
- Internal inspection of BOP cavities (opened as required)
- Internal inspection of annular (dismantled as required)
- Visual inspection and functional test of accumulator unit and its remote stations
- Functional test of the BOPs
- Pressure tests of the BOPs
- Pressure tests of the choke manifold, choke line and kill line and their valves
- Functional test of all other well control equipment
Specialised Coating
Specialty Coatings including Xylan and Everslick
Both Xylan and Everslik are commonly used because of their combination of Corrosion Resistance and Chemical Resistance. Both Are popular in the Oil and Gas sector, but have different applications.
Xylan is a brand name of a range of coatings, each of which can be used for different applications but typically they contain PTFE and offer improved Wear Resistance, Reduced Friction and Heat Resistance. They are most popular as a coating for components that will be used in subsea environments.
Everslik is a dry lubricant coating that is often combined with different materials depending on the application. It’s one of a number of Molybdenum Disulphide based coatings that are supplied under various trade names. Everslik will give your components added protection against corrosion, is low friction, and can operate at a wide range of temperatures.
STSI Facility is at your service to provide you with the most technically advanced forms of industrial coatings.
WE OFFER THE FOLLOWING SPECIALTY COATINGS
- Zinc Phosphate Coating: (for equipment that may be exposed to severe environments)
- Xylan Coating: (generally used to reduce friction and for protection in corrosive environments)
- Everslick Coating: (used for its lubricity and corrosion resistance)
Sand Blasting and Painting
“Sandblasting”, abrasive blasting is the use of abrasive “Media” under high pressure air to erode the surface of an object down to its parent material. Over time, metals by nature oxidize (e.g.. rust) and lose their luster and shine. Depending on the media used, dull metals can be made to look new again. Painted surfaces can be quickly cleaned away saving time and effort. Abrasive blasting is not limited in its use and has many applications to which it can be used with great effect. Grit blasting is ideal for aggressive cleaning applications.
Paint is the most commonly used material to protect steel. The protective paint systems usually consist of primer, undercoat(s) and finish coats. Each coating ‘layer’ in any protective system has a specific function, and the different types are applied in a particular sequence of primer followed by intermediate / build coats in the shop, and finally the finish or topcoat. We verify the paint materials are in compliance with the specification and this includes checking packaging and labelling; verifying the condition of paint in the container; and taking samples for testing. One of the most important inspection tasks we perform during a painting project is measuring the thickness of the paint coat to always make sure it’s the right thickness.
Third Party Inspections
Third Party Inspection Services
- Lifting Inspections
- Rig Inspections
- DROPS
- NDT: Non Destructive Testing Services
- OCTG Inspections
- Pressure Testing and Well Control
- Specialized Coating
- Sand Blasting and Painting
For More Informtion:
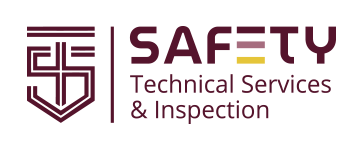